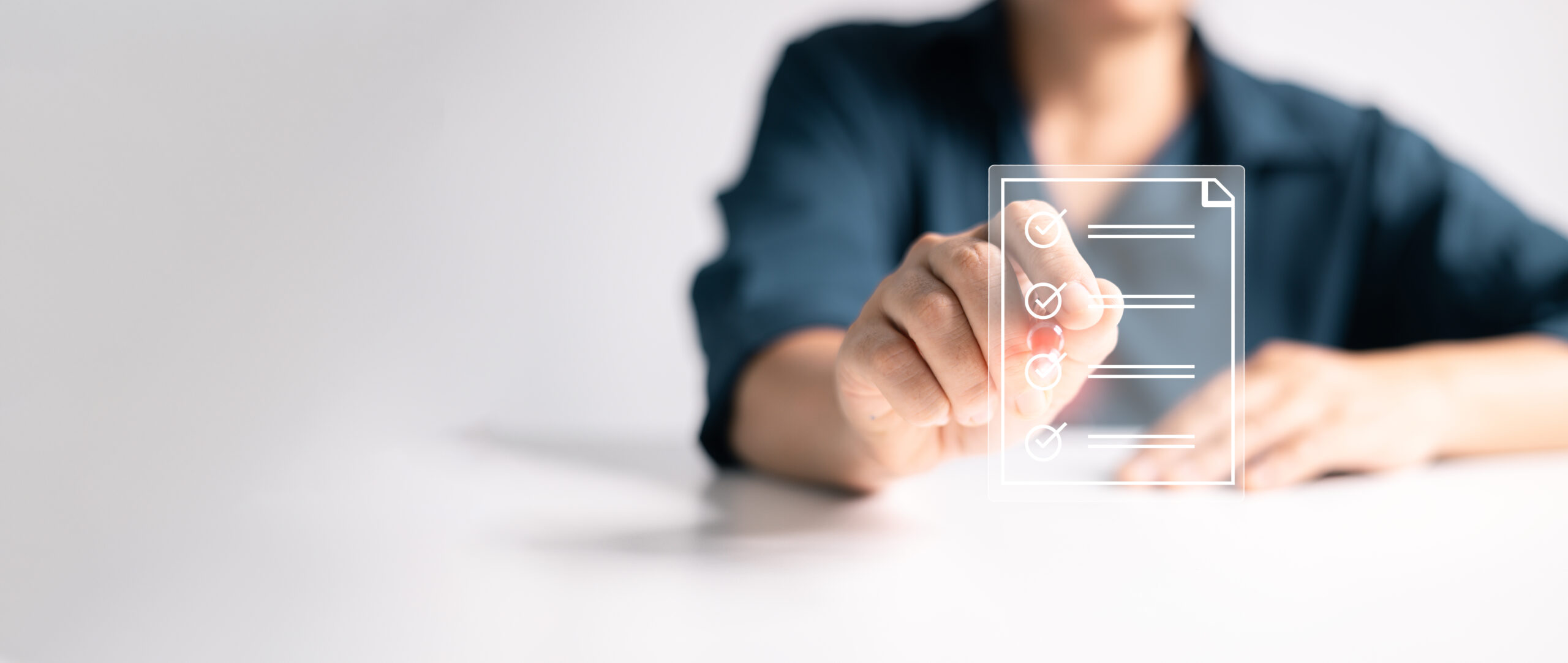
When it comes to ensuring precision and quality in inspection services, selecting the right provider is critical. Asking the right questions can help you determine if your organization and a potential provider are a good match. At Advanced Inspection Services (AIS), we understand the importance of combining expertise, technology, and customer service to meet your unique needs.
With many contract inspection providers available to work with, here are some questions we recommend you ask when evaluating a potential provider to determine if your organizations align.
Top 10 Questions to Ask
1. What types of inspections do you provide?
Industrial inspections can range widely in scope and technique. Ensuring that your provider has the necessary experience and equipment to properly handle your specific application is paramount in achieving your desired results.
AIS offers contract inspection services utilizing a broad range of technologies. We perform everything from First Article Inspections (FAI), GR&R studies, and capability studies in addition to dimensional inspection, reverse engineering, surface & form, and CT scanning inspections.
2. What standards do you follow?
Different industries require adherence to specific standards, and verifying a provider’s standards helps filter out organizations that aren’t a good fit.
AIS, for example, is accredited to the ISO/IEC 17025 standard.
3. Are your technicians certified?
Technician certification is essential to ensure the validity of inspection results. Certified technicians combined with certified equipment and processes can help minimize error and deliver the most accurate results possible.
Each AIS inspector holds GD&T certifications through our partner IIGTD and several hold ASME GDTP Professional certifications in addition to continuous training in their respective specialties.
4. How do you report your findings?
Clear communication on desired data feedback prior to inspection makes for a smooth process and getting the right results the first time. Additionally, knowing the report format you want to receive prior to inspection is helpful in keeping both parties on the same page.
Each inspection performed at AIS comes with a standard report and certificate of inspection that includes detailed insights and recommendations, helping clients make informed decisions about their processes.
5. Have you handled projects similar before?
Experience matters. A provider that has completed projects and solved challenges similar to yours can be an efficient partner to work with. However, if a provider doesn’t have experience with a project like yours but has the tools and capabilities to do so, don’t necessarily count them out! A proven track record of solving complex challenges is a mark of a quality inspection provider.
Whether it’s aerospace and defense, medical device manufacturing, or automotive, AIS has the breadth of experience to handle a wide range of industry-specific inspection challenges.
6. Do you assist with corrective actions?
An inspection provider should not only identify issues but also provide guidance on corrective actions.
Our team goes beyond just reporting, helping customers address any discrepancies and providing recommendations for improvement.
7. What is your turnaround time?
Timeliness is often critical for inspection applications. However, a provider should be committed to delivering results efficiently without compromising accuracy; producing poor quality work to meet promised turnaround times can end up costing you more down the line.
Our combination of state-of-the-art technology, decades of industry experience, and exceptional customer support makes us an efficient choice for contract inspection and metrology solutions.
8. How do you manage traceability in inspection data?
A traceability process ensures that all measurement results are backed by verifiable records, allowing for full documentation records from raw data to final reporting. An inspection provider without a reliable traceability process can result in errors and inaccurate data in the report you receive.
Calibrating regularly, and thus routinely staying in line with standards, helps us maintain consistency in our measurements, with positive implications both internally and externally.
9. What is your process for ensuring equipment calibration accuracy?
Equipment precision is vital to accurate inspections. Understanding how a provider maintains and calibrates their tools can be a key component to confidence in their reliability.
AIS is unique in that our parent organization, Productivity Quality Inc. (PQI), with whom we share a facility, is a metrology equipment and service provider with a dedicated calibration team who maintains the equipment in our lab. The reference tools our calibration team uses are calibrated directly by NIST.
10. How do you stay current with evolving technology and standards?
The inspection industry is constantly evolving. Providers should demonstrate a commitment to continuous improvement through training and investment in new technologies.
Our commitment to quality is evident through our biannual audit and accreditation process. We have been an accredited provider for over 20 years and have grown from 10 accredited services to over 100 accredited inspection parameters, and we add more every year. The equipment in our lab receives consistent maintenance and calibration and our machines are upgraded often. However, our largest testament to staying current is the brand new 7,500 sq. foot environmentally controlled lab we opened at the end of 2024 to fill with the latest tools and technology.
Choosing the right inspection provider is a crucial decision that can impact the quality and success of your projects. By asking these important questions, you can ensure that your organization aligns with a provider capable of delivering precision, expertise, and dependable service. At AIS, we pride ourselves on being more than just a service provider — we’re a partner in your success, committed to helping you meet your most demanding inspection challenges with cutting-edge technology and personalized support.
March 24, 2025